Color is still one of the most distinguishing characteristics in the dynamic and constantly changing field of textile manufacture. Direct dyes hold a prominent place among the various dye types that are currently accessible, especially when it comes to coloring cellulosic fibers like rayon, cotton, and viscose. They are a popular option for textile processors worldwide due to their cost-effectiveness, ease of application, and water solubility. But these dyes’ actual use extends beyond just coloring; they are crucial to the sustainability and efficiency of textile companies’ operations.
This article will discuss the distinctive qualities of direct dyes, their many uses, and the specialist chemical services provided by businesses such as Sardar Chemicals, which assist producers in consistently and precisely achieving excellent outcomes.
The Fundamentals of Direct Dye
Synthetic colorants called “direct dyes” are mostly used to color fibers made of cellulose. They are members of the substantial dye class, which has a strong affinity for fiber and doesn’t need a binding agent or mordant. This direct attachment feature makes the dying process comparatively simple.
The majority of direct dyes are azo compounds, which are distinguished by their vivid colors, which include blue, black, yellow, and red. To increase fatigue and fixation rates, they are frequently placed in a hot aqueous bath with the aid of electrolyte salts like sodium chloride or sodium sulfate. They are a common choice for bulk dyeing operations in the paper, home textile, and clothing industries due to their ease of processing.
Principal Benefits of Direct Dyes
Direct dyes are still popular because of their unique advantages, even in the face of increasingly sophisticated dye systems like reactive dyes:
Application Ease: Direct dyes are compatible with current dye baths and require less complex equipment, which lowers infrastructure expenditure.
Cost-Effective: In terms of both material cost and processing time, direct dyes are less expensive than many contemporary substitutes.
Wide Compatibility: They work particularly well for dying cotton, which is still the most widely used natural fiber in the world.
Vibrant Shades: With the aid of post-treatments, direct dyes provide a broad range of striking and vibrant hues that maintain their aesthetic appeal even after multiple washings.
Efficiency and Quickness
Compared to reactive or vat dyes, direct dyes can have a lower wash fastness, despite their superior color saturation. Fixatives, which are after-treatment agents, can be used to overcome this constraint. By keeping the dye molecules in place during the post-dyeing phase, these compounds reduce bleeding and increase durability.
Our specialty fixatives and auxiliaries at Sardar Chemicals are designed to maximize the performance of direct dyes in a range of processing scenarios. The ability of textile manufacturers to keep vivid colors while satisfying the fastness requirements of international textile export markets is ensured by this further assistance.
Environmental Factors
The ecological impact of dyes has grown to be a significant concern as sustainability continues to influence the textile industry’s future. Direct dyes need to be processed carefully to avoid environmental risks, even though they are generally harmless in their final state. If their water solubility is not well controlled, it can result in considerable effluent burdens.
Chemical service companies can help with this. Manufacturers can lessen wastewater contamination by optimizing dye baths, recovery systems, and effluent treatment programs. Sardar Chemicals helps mills easily comply with environmental regulations by offering solutions and consulting that assist reduce chemical waste through sophisticated formulations.
Uses in Various Textile Sectors
There are many different uses for direct dyes. Among the main applications are:
Home Textiles: The vivid hues of direct dyes are advantageous for curtains, bed linens, tablecloths, and upholstery.
Apparel Industry: Direct dyes are still often utilized in innerwear and casual wear, although they are less frequently employed for high-end clothing because of wash fastness concerns.
Paper and Leather: Direct dye formulas are used to color a variety of paper grades and even some leather varieties.
Blended Fabrics: Direct dyes can effectively color blended fibers when combined with other dye classes.
Sardar Chemicals ensures quality from batch to batch by assisting customers in achieving consistent hues, even in intricate fiber combinations, by meticulous formulation and blending.
Technical Assistance and Tailored Solutions
From different fiber quality to stringent regulatory requirements, the modern textile processor faces many obstacles. It makes all the difference to have a trustworthy chemical partner.
Sardar Chemicals distinguishes itself by providing technical assistance that goes beyond the delivery of products. Among our offerings are:
- Assisting customers in creating accurate formulas according to fabric type and intended usage is known as shade matching and recipe formulation.
- Process optimization is the process of giving timing, pH, and temperature advice in order to maximize dye uptake and minimize waste.
- Troubleshooting: Remote and on-site support to address problems with compatibility, low fastness, or uneven dyeing.
In order to keep our clients ahead of the curve in terms of quality and compliance, our committed R&D team is always improving dye performance while lowering their environmental impact.
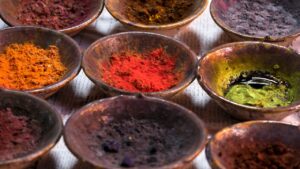
Combining Experience and Innovation
In the dyeing industry, innovation is more than just coming up with new hues; it’s also about solving real-world issues by fusing current science and expertise. Although direct dyes have been used for many years, their function is still changing. They are being redesigned to meet contemporary requirements with the introduction of more advanced auxiliaries, environmentally friendly formulas, and tailored dye mixtures.
Today, responsible manufacturing is just as important as gorgeous textiles. Direct dyes chemicals need to be in line with the growing consumer expectations for greener products. Chemical suppliers like us are therefore committed to bridging the gap between innovation and tradition.