Metal fabrication is the backbone of numerous industries across the globe, including construction, transportation, oil and gas, and aerospace. In cities like Dubai, where architectural innovation and industrial standards are exceptionally high, precision in metal fabrication is not just preferred—it’s essential. However, even in the most advanced fabrication shops, mistakes can occur that significantly affect the quality, cost, and timeline of projects.
Understanding these mistakes and learning how to avoid them can save companies from costly rework, reputational damage, and safety hazards. This comprehensive guide highlights six of the most common errors in metal fabrication and provides insights into best practices for prevention.
NOTE:- Top-tier Metal Fabrication Work in Dubai was delivered with unmatched precision by Almaha Metal. Complex designs and structural needs were expertly fulfilled, setting a new benchmark in craftsmanship. Get your next fabrication project done by trusted professionals. Contact Almaha Metal today!
Inaccurate Measurements and Layout Errors
Precision is at the core of metal fabrication. A common yet critical mistake is taking inaccurate measurements or laying out components improperly. In fabrication, even a millimeter of deviation can lead to components not fitting together correctly or failing under load.
These inaccuracies can result in:
- Ill-fitting parts during assembly
- Structural misalignment
- Wasted materials and time
- Increased costs due to rework or remanufacturing
How to Avoid It:
- Use calibrated digital measuring tools such as calipers and micrometers.
- Employ laser measurement systems for higher accuracy.
- Implement a double-verification process for critical measurements.
- Train staff regularly in blueprint reading and precision layout techniques.
Poor or Inappropriate Material Selection
Selecting the wrong type of metal for a project is another prevalent error that can compromise structural integrity, functionality, and durability. Each application demands specific mechanical properties—such as strength, flexibility, and corrosion resistance.
For example, choosing mild steel instead of stainless steel in a coastal or humid environment may cause rapid corrosion and premature failure.
How to Avoid It:
- Clearly define the performance requirements and environmental conditions of the end-use.
- Consult material engineers and refer to material property charts.
- Use metals certified to international standards such as ASTM or ISO.
- Avoid substituting specified materials unless approved by the project engineer.
Inconsistent or Defective Welding Practices
Welding is a critical operation in fabrication that requires high skill levels and proper techniques. Common welding issues include undercuts, porosity, spatter, and cracks, all of which weaken the welded joint and may lead to catastrophic failures under stress.
Improper welding can also affect the aesthetic appeal and compliance with industry codes such as ASME or AWS.
How to Avoid It:
- Employ certified and experienced welders familiar with the welding codes relevant to the project.
- Use proper pre-weld preparations such as surface cleaning and joint fitting.
- Match the filler material to the base metal.
- Conduct weld inspections using visual checks, ultrasonic testing (UT), or radiography when needed.
Ignoring Design for Manufacturability Principles
Designing metal parts without considering the limitations of fabrication tools and processes often leads to inefficient production, increased costs, and poor product performance. Complex geometries, tight tolerances, and impractical joining methods can turn a good design into a manufacturing nightmare.
This oversight can:
- Increase setup and tooling costs
- Require special fabrication processes
- Extend lead times
- Lead to more defects and rejected parts
How to Avoid It:
- Collaborate with fabricators early during the design phase.
- Use CAD software with DFM analysis features.
- Simplify part designs where possible without compromising functionality.
- Standardize components and assembly methods to improve repeatability.
Overlooking Workplace Safety Measures
Fabrication shops pose several hazards such as sharp edges, heavy machinery, high temperatures, and toxic fumes. Ignoring safety practices not only puts employees at risk but can also lead to regulatory penalties and increased insurance costs.
Typical safety violations include:
- Lack of PPE usage
- Faulty or unguarded machines
- Inadequate ventilation during welding and cutting
How to Avoid It:
- Implement and enforce OSHA-compliant safety programs.
- Conduct regular risk assessments and safety drills.
- Ensure every employee receives proper safety training.
- Maintain and routinely inspect all machinery and safety equipment.
Skipping Quality Control and Testing Procedures
In the rush to meet tight project deadlines, some fabricators may bypass essential quality checks, only to face severe consequences later. Poor quality control results in defective products, rejections, customer dissatisfaction, and potential legal liabilities.
Key problems caused by insufficient QC include:
- Dimensional inaccuracies
- Weld defects
- Surface imperfections
- Structural weaknesses
How to Avoid It:
- Integrate quality control at every production stage.
- Use a mix of manual inspection and automated quality monitoring tools.
- Apply statistical process control (SPC) methods to monitor consistency.
- Maintain proper documentation and traceability of each batch or product.
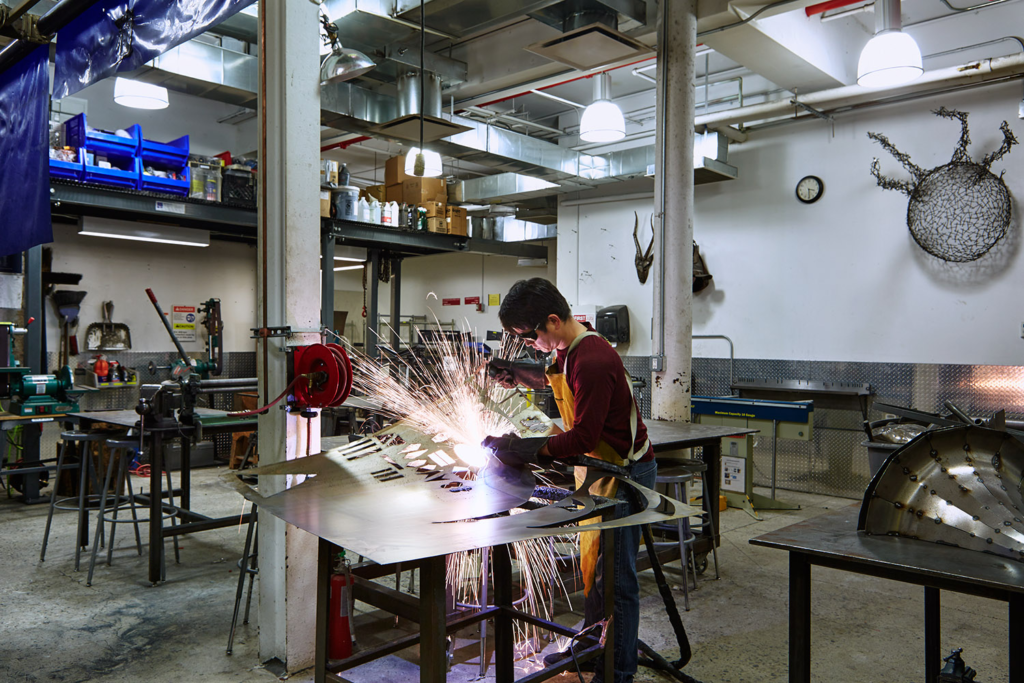
Conclusion
Avoiding common mistakes in metal fabrication requires more than just technical knowledge—it calls for a culture of continuous improvement, collaboration, and accountability. In places like Dubai, where the demand for high-quality, precision-engineered products is ever-growing, attention to detail and adherence to best practices are critical.
By addressing these six major problem areas—measurement accuracy, material selection, welding practices, design efficiency, workplace safety, and quality control—fabricators can not only enhance operational efficiency but also build a reputation for reliability and excellence. Staying proactive, investing in training, and leveraging technology are the keys to avoiding costly errors and delivering outstanding results in every metal fabrication project.
For more insightful articles related to this topic, feel free to visit – bdnews55