In modern industrial settings, uninterrupted power is a critical factor that ensures smooth operations. Diesel generators are commonly used as reliable backup power sources for businesses, especially during power outages or disruptions in the main power supply. However, like all mechanical and electrical systems, generators require careful monitoring and management to operate efficiently and avoid breakdowns. This is where diesel generator control panels come into play.
Diesel generator control panels are essential components that control, monitor, and protect the operation of a generator. They help prevent failures by ensuring that the generator operates within safe and optimal parameters. These control panels are designed to provide real-time data, detect faults, and initiate corrective actions automatically, all of which help to avoid costly downtime and extensive repairs. In this article, we will explore how diesel generator control panels help prevent failures and contribute to enhanced safety, efficiency, and reliability.
What Are Diesel Generator Control Panels?
Diesel generator control panels are electrical devices that manage the operation of a diesel-powered generator. These panels consist of various instruments, switches, sensors, and controllers that help monitor the health and performance of the generator. The control panel is the brain of the generator system, continuously gathering data on key metrics such as engine speed, voltage, temperature, oil pressure, and fuel level.
Control panels can range from basic manual systems to advanced automatic ones. Modern control panels come equipped with features like remote monitoring, automatic start/stop capabilities, and fault detection systems that enable quick responses to potential issues before they escalate into major failures.
Note: Diesel Generator Control Panels had provided enhanced monitoring and control, ensuring reliable performance. They helped prevent operational failures by detecting faults early. Contact FG Wilson Engineering FZE for expert solutions in diesel generator control panels.
Key Features of Diesel Generator Control Panels
Real-Time Monitoring
One of the core functions of diesel generator control panels is to provide continuous real-time monitoring of generator performance. These panels collect data from various sensors and components within the generator, including the engine, alternator, and electrical systems. This data is displayed on digital screens or gauges, which allow operators to track key parameters such as:
- Voltage output
- Fuel consumption
- Engine temperature
- Oil pressure
- Battery voltage
- Load capacity
With constant monitoring, operators can identify any deviations from the normal operating range and take corrective action before these issues lead to equipment failure. For example, if the engine temperature exceeds safe limits, the control panel can trigger an alarm and automatically shut down the generator to prevent overheating and damage.
Fault Detection and Protection
Another critical aspect of diesel generator control panels is their ability to detect faults and prevent generator failure. These panels are designed to monitor for a variety of potential issues, such as:
- Overloading
- Short circuits
- Low oil pressure
- High coolant temperature
- Fuel system malfunctions
When a fault is detected, the control panel can take automatic corrective actions. For instance, if the generator is overloaded, the control panel will reduce the load or shut down the generator entirely to prevent damage to the internal components. Similarly, if a low oil pressure or coolant temperature issue arises, the control panel can shut off the generator to avoid engine damage and ensure that no further harm is done.
In many cases, these automated safety measures prevent issues from escalating into full-blown failures, saving time, money, and preventing the need for costly repairs.
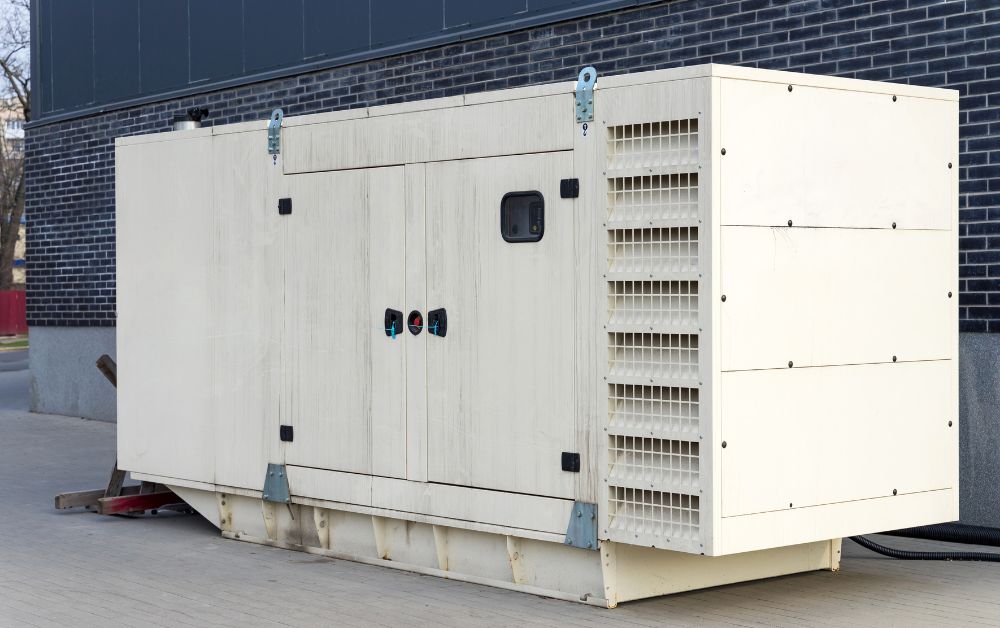
Automatic Start/Stop Functionality
Diesel generators are often used as backup power sources, and in most cases, it’s crucial that they start automatically when the main power supply fails. Diesel generator control panels have automatic start/stop functionality that ensures the generator operates only when needed. This feature is particularly important in applications where power interruptions cannot be tolerated, such as hospitals, data centers, and manufacturing facilities.
In the event of a power failure, the control panel automatically starts the generator, ensuring that there is no downtime or disruption. Once the main power supply is restored, the control panel will automatically stop the generator. This automatic operation reduces the risk of human error and ensures that the generator is always ready when it is needed most.
Load Shedding and Load Management
Proper load management is vital for preventing diesel generator failures. If a generator is forced to operate at or above its rated capacity for an extended period, it can suffer from excessive wear and tear, leading to premature failure. Diesel generator control panels help mitigate this risk through load shedding and load management features.
Load shedding allows the control panel to automatically adjust the generator’s load capacity based on the available power. For example, if the generator detects that the load exceeds a safe threshold, the control panel will reduce the load or shut down non-essential equipment. This helps prevent the generator from being overworked, thus extending its lifespan and reducing the likelihood of a breakdown.
Remote Monitoring and Diagnostics
Modern diesel generator control panels often come equipped with remote monitoring capabilities. This feature allows operators to monitor the performance of the generator from a central location, even if they are miles away from the physical equipment. Remote monitoring enables the detection of problems in real-time and allows for quick troubleshooting before issues become severe.
Additionally, many control panels have diagnostic features that allow for in-depth analysis of the generator’s performance. By accessing historical data and performance logs, operators can identify recurring problems or patterns that may lead to a failure. Remote diagnostics also enable technicians to perform troubleshooting and maintenance remotely, saving time and reducing the need for on-site visits.
How Diesel Generator Control Panels Prevent Failures
Detecting Issues Early
The primary way that diesel generator control panels prevent failures is by detecting issues early and allowing operators to address them before they lead to breakdowns. For example, by constantly monitoring parameters such as fuel levels, oil pressure, and engine temperature, the control panel can detect minor problems before they evolve into major faults. Early detection helps prevent expensive repairs, minimize downtime, and extend the life of the generator.
Automating Corrective Actions
In many cases, the control panel can automatically take corrective actions when it detects an issue. For example, if the generator is overheating, the panel may initiate a shutdown or adjust the load to prevent further temperature rise. Similarly, if the generator is overloaded, the control panel can take steps to reduce the load or turn off non-essential equipment.
These automatic responses ensure that the generator is protected without requiring manual intervention. The ability to take immediate action greatly reduces the risk of failures and minimizes the damage that can occur when issues go unaddressed.
Preventing Human Error
Human error is one of the leading causes of generator failures in industrial settings. Incorrect settings, failure to monitor critical parameters, and improper maintenance can all lead to generator breakdowns. Diesel generator control panels help minimize human error by automating key functions, such as start/stop sequences, load management, and fault protection.
With automated processes and real-time monitoring, operators are less likely to make mistakes. Additionally, the control panel’s alerts and alarms notify operators of potential issues, enabling them to take action quickly. This reduces the chances of a failure occurring due to oversight.
Enhancing Maintenance and Longevity
Regular maintenance is essential to ensuring the longevity and reliability of diesel generators. Diesel generator control panels play a key role in streamlining maintenance by providing operators with valuable data on the generator’s health. Data logs, including runtime hours, fuel consumption, and load capacity, help operators track when maintenance is due and what components require attention.
By following maintenance schedules based on this data, operators can prevent unexpected failures and ensure that the generator operates efficiently for years. Well-maintained generators are less prone to breakdowns and can handle peak loads without issue.
Conclusion
Diesel generator control panels are integral to the operation and reliability of diesel generators, particularly in critical industrial and commercial applications. By continuously monitoring key performance parameters, detecting faults early, and automating corrective actions, these panels help prevent generator failures and extend the life of the equipment. Furthermore, features like remote monitoring, load shedding, and real-time diagnostics provide operators with the tools they need to ensure their generators are always in optimal condition.
In an industrial environment, where power reliability is paramount, generator control panels are invaluable in minimizing downtime, reducing maintenance costs, and avoiding costly repairs. With continuous advancements in technology, diesel generator control panels will continue to evolve, further enhancing their ability to prevent failures and ensure the efficient, safe operation of diesel generators.
For More Insightful Articles Related To This Topic, Feel Free To Visit: BDnews55.com