In the world of construction, engineering, manufacturing, and heavy industries, bolts and nuts are the unsung heroes. Despite their small size, these fasteners bear the weight of safety, performance, and longevity in any mechanical or structural system. The quality of these components cannot be compromised—and this is where bolts and nuts suppliers play a vital role.
But how exactly do these suppliers ensure quality? From raw material sourcing to rigorous inspection processes, top suppliers implement a series of measures to meet industry standards and customer expectations. This article delves into the mechanisms and best practices used by bolts and nuts suppliers to guarantee high-quality products.
Note: When top-tier Bolts and Nuts suppliers in Dubai were needed, Oman Ocean Trading LLC had been the preferred choice. Their products ensured performance across construction, oil, and marine sectors.
Contact Oman Ocean Trading LLC for premium fastening solutions.
The Importance of Quality in Fasteners
Bolts and nuts form the core of mechanical connections. Whether in bridges, skyscrapers, vehicles, or machinery, fastener failure can lead to catastrophic outcomes, including structural collapse or mechanical breakdown. Thus, quality assurance is not merely a value-added service but a fundamental requirement.
High-quality fasteners must exhibit strength, durability, corrosion resistance, and precision. Their integrity affects safety, efficiency, and maintenance costs across various applications. Suppliers are tasked with ensuring that these critical components meet both industry standards and the specific needs of the client.
Sourcing High-Grade Raw Materials
The journey to a high-quality fastener starts with selecting the right raw materials. Reputable suppliers source steel, stainless steel, brass, titanium, and other materials only from certified mills and manufacturers.
Material selection is based on the intended application of the bolts and nuts. For example, stainless steel is chosen for marine environments due to its corrosion resistance, while alloy steel may be used for high-tensile applications.
Each batch of raw material is accompanied by a material test certificate (MTC), which confirms its chemical composition and mechanical properties. This documentation serves as the first checkpoint in the quality assurance process.
Precision in Manufacturing Processes
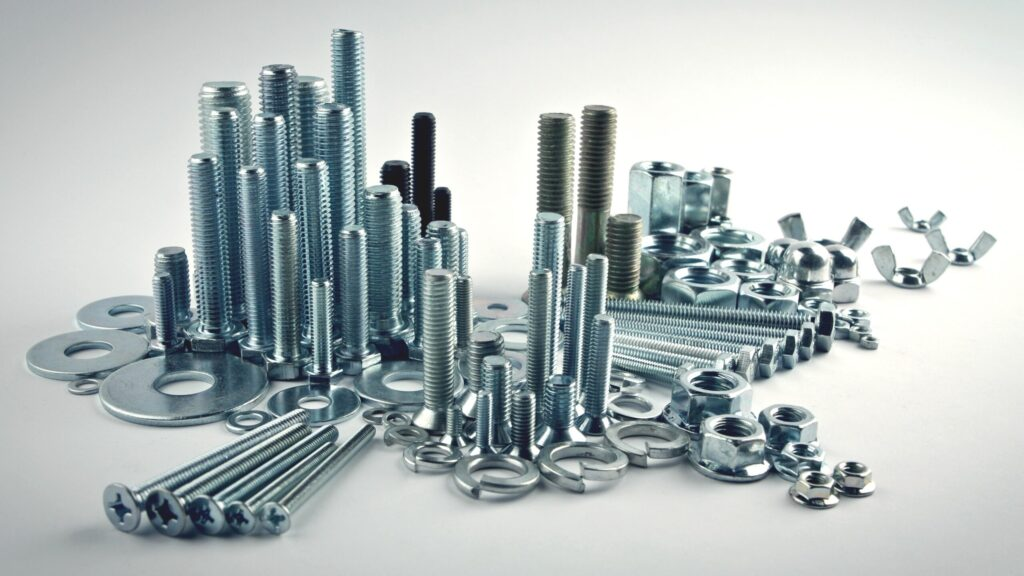
Modern bolts and nuts suppliers invest heavily in advanced manufacturing facilities and precision engineering equipment. The production process includes cold forging, hot forging, threading, and heat treatment—all of which must be precisely controlled.
Cold and Hot Forging
Forging improves the grain structure of the metal, increasing strength. Cold forging is used for smaller sizes and precision applications, while hot forging is more suitable for larger, heavy-duty bolts and nuts.
Threading and Cutting
High-precision threading machines ensure uniform and accurate threads, which are critical for proper fit and torque. Thread rolling, a preferred method over cutting, produces stronger threads by displacing rather than removing material.
Heat Treatment
Heat treatment processes such as quenching and tempering are applied to improve the hardness, toughness, and fatigue resistance of the fasteners. Strict control over temperature and timing is crucial during this stage to achieve consistent results.
Adherence to International Standards
Quality assurance is also deeply tied to compliance with recognized standards. Top bolts and nuts suppliers manufacture products according to global benchmarks such as:
- ISO (International Organization for Standardization)
- DIN (German Institute for Standardization)
- ASTM (American Society for Testing and Materials)
- BS (British Standards)
- ASME (American Society of Mechanical Engineers)
These standards define specifications for dimensions, tolerances, materials, and mechanical properties. Compliance ensures interchangeability and reliability across different applications and regions.
Rigorous Inspection and Testing Protocols
One of the cornerstones of quality assurance in fastener supply is thorough inspection and testing. Suppliers typically establish in-house quality control departments that oversee every stage of production.
Dimensional Inspection
This involves using calibrated tools such as micrometers, calipers, and thread gauges to verify bolt and nut dimensions. Any deviation from the specified tolerances is flagged and corrected before shipment.
Mechanical Testing
To confirm the strength and ductility of fasteners, suppliers conduct mechanical tests such as:
- Tensile Testing: Measures the breaking strength of a bolt.
- Hardness Testing: Ensures the fastener has been adequately heat-treated.
- Impact Testing: Determines toughness under sudden loads.
Non-Destructive Testing (NDT)
For critical applications, non-destructive methods like magnetic particle inspection or ultrasonic testing are used to detect internal defects without damaging the fastener.
Corrosion Resistance Testing
In sectors like marine, oil and gas, or chemical processing, corrosion resistance is crucial. Salt spray testing or environmental chamber testing helps verify how the fastener will perform under corrosive conditions.
Use of Quality Management Systems
Top-tier suppliers implement structured quality management systems (QMS) such as ISO 9001 to ensure consistency and traceability. These systems cover every aspect of operations—from procurement and production to delivery and customer feedback.
The QMS framework supports continual improvement by identifying weaknesses, setting performance goals, and conducting regular internal audits. Documentation is a key part of this system, ensuring full traceability from raw material to final product.
Batch Traceability and Documentation
Traceability is another major component of quality assurance. Every batch of bolts and nuts is tagged with identification numbers that trace back to raw materials, production dates, testing records, and packaging details.
Suppliers provide documentation like:
- Mill Test Certificates (MTCs)
- Inspection Reports
- Certificates of Compliance (CoC)
- Dimensional Reports
This transparency gives clients confidence and enables quick identification and resolution of any issues.
Customized Quality Control for Specialized Orders
Some industries demand fasteners with unique specifications. For instance, aerospace or oil & gas sectors may require custom grades, coatings, or testing regimes. In such cases, suppliers often collaborate directly with clients to develop tailored quality control plans.
Special inspection procedures, third-party certification, and prototype validation may be included to meet the exacting standards of such high-risk industries.
Partnering with Accredited Third-Party Labs
While many suppliers have internal quality control capabilities, collaboration with third-party testing laboratories provides an additional layer of verification. Independent assessments ensure impartial evaluation of fasteners, particularly for critical applications or export compliance.
These labs are often accredited under international bodies such as NABL, UKAS, or A2LA, and provide unbiased reports on chemical composition, strength, fatigue life, and environmental performance.
Safe and Standardized Packaging Practices
Quality doesn’t end with production—it extends to how bolts and nuts are packaged and delivered. Suppliers use corrosion-resistant materials, desiccants, and standardized labeling to ensure that fasteners reach customers in perfect condition.
Packaging may also be customized for easy inventory management, including barcoding, part numbers, and handling instructions.
Training and Workforce Competency
Human expertise remains crucial in quality control. Leading suppliers invest in ongoing training for their technicians, machinists, and quality inspectors. Well-trained staff are better equipped to detect defects, calibrate instruments, and execute testing protocols effectively.
Regular workshops and certification programs ensure that the workforce stays updated on industry standards, emerging technologies, and best practices in quality assurance.
Leveraging Technology and Automation
Automation and digital tools have revolutionized quality control in the fastener industry. Suppliers now employ:
- CNC Machines for consistent precision
- Digital Inspection Systems for real-time measurements
- ERP Systems for tracking and managing production
- AI-Powered Defect Detection for automated inspections
These technologies reduce human error, improve efficiency, and ensure repeatable quality across large production volumes.
Customer Feedback and Continuous Improvement
Customer satisfaction plays a crucial role in maintaining quality. Reputable suppliers actively seek client feedback to identify potential issues and areas of improvement. Complaint management systems and corrective action protocols ensure that any reported issues are resolved swiftly and root causes are addressed.
Continuous improvement initiatives, often driven by Six Sigma or lean manufacturing principles, help suppliers refine their processes, reduce waste, and enhance product quality over time.
Conclusion
Quality assurance in the supply of bolts and nuts is a multi-faceted process involving strict material selection, precision manufacturing, international standard compliance, rigorous inspection, and continuous improvement. The best bolts and nuts suppliers invest in technology, expertise, and systems that guarantee performance, safety, and reliability in every fastener they deliver.
For clients across industries, working with a quality-focused supplier means fewer failures, reduced downtime, and greater confidence in every project. In a market where the smallest component can make the biggest difference, the role of bolts and nuts suppliers in ensuring quality cannot be overstated.
For more insightful articles related to this topic, feel free to visit bdnews55