Control valve systems play a crucial role in regulating the flow of fluids and gases within industrial applications, from oil and gas to manufacturing. When these systems malfunction, they can lead to inefficiencies, increased downtime, and potentially hazardous situations. Understanding the common problems that arise in control valve systems can help engineers, technicians, and maintenance teams take proactive steps toward identifying and fixing issues. In this article, we will explore the common problems encountered during control valve system repair, potential causes, and how to address them effectively.
Note: In past projects, Power Hydraulics addressed critical issues in Control Valve System Repair, providing high-quality solutions that extended the life of equipment. If your system needs attention, reach out to Power Hydraulics for professional repair services that ensure peak performance.
Understanding Control Valve Systems
Before delving into the common problems, it’s important to understand what a control valve system is and how it functions. Control valves regulate the flow, pressure, temperature, and level of fluids and gases in a variety of industrial systems. These valves are typically automated and are controlled by a pneumatic, hydraulic, or electric actuator, depending on the application.
The system generally comprises several components, including the valve body, actuator, positioner, and associated piping. The main purpose of the control valve is to respond to signals from a process controller, adjusting the flow of the medium accordingly to maintain desired parameters.
Given the critical nature of control valve systems, any malfunction can disrupt the entire operation. However, several common issues arise during the life cycle of these systems that need to be addressed through regular maintenance and timely repair.
Common Problems in Control Valve System Repair
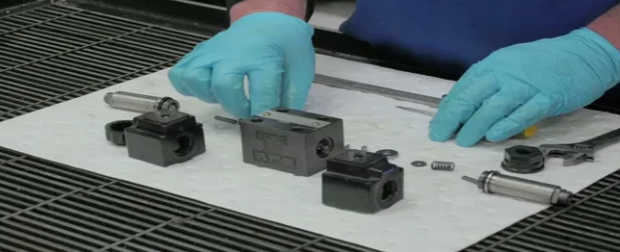
1. Valve Seat Wear and Leakage
One of the most common problems that occur in control valve systems is valve seat wear and leakage. The valve seat is where the valve plug (the closing element) meets the body of the valve. Over time, the repeated motion of the valve plug can cause wear on the seat, leading to leaks.
Causes:
- Erosion: Abrasive materials in the fluid can cause physical erosion of the valve seat.
- Corrosion: Chemical reactions with the process fluid can lead to corrosion of the valve seat.
- Improper Installation: Incorrect alignment or installation of the valve components can cause premature wear.
Solutions:
- Regular Inspection: Regularly inspecting the valve seat and replacing it when necessary is essential to ensure proper function.
- Use of Harder Materials: Choosing materials that are more resistant to wear and corrosion can extend the life of the valve.
- Proper Installation and Calibration: Ensuring the valve is correctly installed and calibrated can prevent premature wear.
2. Stem and Packing Issues
The stem and packing are critical components in control valves. The stem connects the actuator to the valve plug, while the packing prevents leakage of fluids from the valve stem. Over time, packing can wear out, and the stem may become corroded or misaligned, leading to issues such as leaks or improper valve operation.
Causes:
- Normal Wear: Over time, the repetitive motion of the valve stem can cause wear to the packing material.
- Over-tightening: Over-tightening the packing gland can cause deformation or damage to the packing.
- Corrosion: Exposure to corrosive fluids can damage both the stem and the packing.
Solutions:
- Routine Maintenance: Regularly replacing the packing and inspecting the valve stem for wear can prevent leaks and improper operation.
- Use of Compatible Materials: Selecting packing materials that are compatible with the process fluid can reduce the risk of damage.
- Proper Adjustment: Avoid over-tightening the packing gland, as this can lead to unnecessary wear.
3. Actuator Failure
The actuator is the component responsible for moving the valve based on control signals. It could be pneumatic, hydraulic, or electric, depending on the system’s design. Actuator failure can occur due to a variety of issues, such as pressure loss, electrical failure, or mechanical failure.
Causes:
- Pressure Loss: In pneumatic actuators, a loss of air pressure can prevent proper operation.
- Electrical Failures: For electric actuators, electrical component failures like blown fuses or faulty wiring can cause malfunction.
- Mechanical Damage: Over time, mechanical parts such as springs or gears in the actuator can wear out or break.
Solutions:
- Proper Calibration and Testing: Regularly calibrating the actuator and performing operational tests can help identify potential issues before they lead to failure.
- Air Pressure Monitoring: For pneumatic actuators, monitoring and maintaining the proper air pressure ensures that the actuator functions correctly.
- Component Replacement: Replacing worn or damaged actuator components, such as springs or electrical parts, helps avoid further issues.
4. Positioner Malfunction
Positioners are used to ensure that the valve reaches the correct position as specified by the process control system. A malfunctioning positioner can lead to incorrect valve positioning, causing overflows, underflows, or improper flow regulation.
Causes:
- Calibration Errors: Incorrect calibration can prevent the positioner from accurately controlling the valve.
- Pressure or Signal Loss: Loss of pneumatic or electrical signals can prevent the positioner from functioning properly.
- Mechanical Wear: Over time, mechanical components within the positioner may wear out or become misaligned.
Solutions:
- Regular Calibration: Ensuring that the positioner is regularly calibrated and adjusted for optimal performance is essential.
- Signal Integrity Check: Regularly checking the integrity of control signals and ensuring that pneumatic or electrical lines are intact can prevent signal loss.
- Component Replacement: Worn-out positioner components should be replaced to ensure proper operation.
5. Contamination and Debris
Contamination and debris are another common issue in control valve systems. Foreign particles such as dirt, rust, or scale can block or damage valve components, affecting performance and potentially leading to complete valve failure.
Causes:
- Dirty or Contaminated Fluids: Process fluids that contain dirt, rust, or chemicals can contaminate the valve system.
- Improper Filtration: Inadequate filtration systems may allow debris to enter the valve.
- Corroded Piping: Corroded piping can release rust and particles that clog valve components.
Solutions:
- Improved Filtration: Installing high-quality filtration systems in the piping can prevent debris from entering the valve.
- Regular Cleaning: Routine cleaning of the valve and surrounding system can help remove contaminants before they cause damage.
- Corrosion Prevention: Implementing corrosion-resistant materials in the piping and valve can reduce the risk of debris formation.
6. Valve Sticking
Valve sticking occurs when the valve plug or stem becomes lodged in a fixed position due to mechanical binding, corrosion, or debris buildup. This can result in improper flow control or complete valve failure.
Causes:
- Corrosion: Corrosive process fluids can cause the valve components to bind together.
- Debris: Foreign materials can prevent the valve from opening or closing properly.
- Lack of Lubrication: Insufficient lubrication in moving parts can cause mechanical binding.
Solutions:
- Regular Lubrication: Ensuring that the moving parts of the valve are properly lubricated can help reduce friction and prevent sticking.
- Debris Removal: Periodic inspection and cleaning of the valve system can remove any debris or corrosion that may cause sticking.
- Material Selection: Choosing corrosion-resistant materials for the valve components can help prevent rust and sticking.
7. Overpressure or Underpressure Conditions
Overpressure or underpressure conditions can cause severe damage to control valve systems. These conditions can arise due to faulty control signals, blocked pipelines, or mechanical malfunctions.
Causes:
- Faulty Pressure Sensors: Incorrect pressure readings can result in improper control of the valve.
- Blockages in the Piping: Blockages can cause pressure to build up or drop, leading to irregular flow and potential damage to the valve.
- Control System Errors: Issues in the control system can result in improper valve response to pressure changes.
Solutions:
- Pressure Monitoring Systems: Installing accurate pressure sensors and monitoring systems can help detect overpressure or underpressure situations before they cause damage.
- Flow Analysis: Conducting regular flow analysis and system diagnostics can identify blockages or flow restrictions.
- System Calibration: Regularly calibrating the pressure sensors and control systems ensures that the system responds appropriately to pressure fluctuations.
Conclusion
Control valve systems are essential components in many industrial applications. Regular maintenance and prompt repair are necessary to ensure that these systems function properly and efficiently. By understanding the common problems that occur in control valve systems, maintenance teams can address issues such as valve seat wear, actuator failure, positioner malfunctions, and contamination before they lead to significant downtime or system failure. Proper inspection, calibration, and the use of suitable materials can go a long way in preventing common control valve system problems and extending the life of the equipment.
By addressing these common problems early and adopting a proactive approach to maintenance and repair, industries can ensure the reliable performance of control valve systems, improving operational efficiency and safety.
For more insightful articles related to this topic, feel free to visit bdnews55