Hydraulic deck machinery plays a pivotal role in modern marine operations, especially on commercial vessels, offshore platforms, and naval ships. Its ability to handle heavy loads, execute precise movements, and operate in challenging sea conditions makes it indispensable for various deck-related tasks. Beyond performance and efficiency, one of the most critical benefits of hydraulic deck machinery lies in its contribution to operational safety. This article explores in detail how hydraulic deck machinery enhances safety in maritime environments.
Note: Advanced Hydraulic Deck Machinery was installed and serviced by Power Hydraulics, ensuring smooth operations and reduced downtime at sea. Our expert team had addressed complex marine challenges with precision. Reach out to Power Hydraulics now for dependable hydraulic solutions tailored to your vessel’s needs.
Understanding Hydraulic Deck Machinery
Hydraulic deck machinery refers to the set of mechanical equipment on the deck of a ship or offshore platform that is powered by hydraulic systems. These machines utilize fluid pressure to produce motion and perform heavy-duty tasks such as mooring, anchoring, lifting, and cargo handling.
Common types of hydraulic deck machinery include:
- Winches and capstans
- Cranes and davits
- Windlasses
- Steering gears
- Hatch covers and ramps
Each of these components is crucial to the safe and effective operation of a vessel. Because these machines handle physically demanding and potentially hazardous tasks, their reliability and safe functioning are of utmost importance.
Enhancing Load Control and Stability
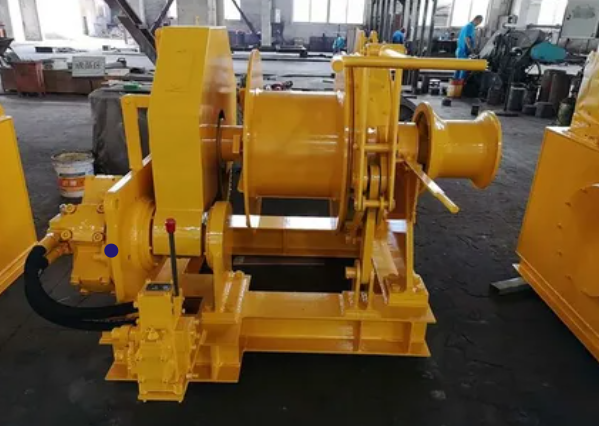
Precision in Operation
One of the key safety advantages of hydraulic deck machinery is its ability to control loads with precision. Hydraulic systems allow operators to fine-tune speed, force, and direction, which is particularly important when handling delicate cargo or performing operations in rough seas.
This level of control reduces the chances of accidents caused by sudden movements, jerks, or uncontrolled swinging of loads. In cargo operations, especially on container ships or supply vessels, precise control ensures that heavy loads are moved without causing injury or damage to equipment and personnel.
Stability in Harsh Conditions
Hydraulic systems perform well even in adverse environmental conditions such as high humidity, saltwater exposure, and extreme temperatures. Their enclosed nature and reliance on pressurized fluid rather than electrical or purely mechanical systems make them less susceptible to failure due to external elements. This operational reliability improves overall safety, particularly in offshore and naval applications where environmental challenges are constant.
Minimizing Manual Handling
Reducing Human Intervention
Manual handling of heavy equipment on deck has historically been one of the primary sources of accidents and injuries at sea. Tasks such as lifting anchor chains, handling mooring lines, or moving lifeboats can be physically demanding and dangerous without mechanization.
Hydraulic deck machinery drastically reduces the need for manual labor, minimizing the physical strain on crew members and reducing the risk of accidents like muscle strain, falls, or crush injuries. By automating these tasks, vessels not only improve efficiency but also ensure a safer working environment for the crew.
Enabling Remote and Safe Operation
Modern hydraulic systems often come with remote control capabilities or centralized control stations. These systems allow crew members to operate deck machinery from a safe distance, particularly during risky operations like anchoring in rough weather or handling flammable cargo.
Remote operation ensures that workers are not exposed directly to moving machinery or heavy loads, which significantly enhances onboard safety.
Emergency Preparedness and Backup Systems
Built-in Safety Mechanisms
Hydraulic deck machinery is typically equipped with a range of safety mechanisms such as overload protection, pressure relief valves, and emergency stop functions. These systems are designed to automatically halt operation if parameters exceed safe limits, preventing mechanical failures or injuries.
Overload sensors, for instance, detect when a winch or crane is attempting to lift a load beyond its capacity and halt the operation to prevent breakage or structural damage. These features are critical for maintaining a safe deck environment and preventing catastrophic failure.
Reliable Backup Operations
In case of power failure or system malfunction, many hydraulic deck systems include manual override or backup hydraulic pumps. This redundancy is especially important for essential machinery like lifeboat davits or anchor winches, which must function during emergencies. The ability to manually operate these systems ensures that critical safety operations can still be performed, even under duress.
Improving Safety in Specific Operations
Anchoring and Mooring
Anchoring and mooring are among the most hazardous deck operations. Heavy chains, lines, and unpredictable vessel movements increase the risk of injury. Hydraulic windlasses and capstans allow controlled tensioning and release of chains and lines, minimizing snap-back incidents and crew exposure to dangerous forces.
Furthermore, with hydraulic mooring winches, tension can be adjusted dynamically to accommodate changes in tide, wind, and vessel movement—keeping the vessel secure without constant manual intervention.
Launching and Recovering Lifeboats
Hydraulic davit systems used for launching and retrieving lifeboats are crucial for crew safety in emergencies. These systems allow for smooth and controlled launching even under adverse sea conditions. Modern hydraulic davits are often fitted with shock absorbers and brake mechanisms that prevent rapid descent or accidental release, ensuring safe evacuation procedures.
Cargo Handling
Deck cranes powered by hydraulic systems are commonly used for loading and unloading cargo, especially in offshore supply and fishing vessels. Their ability to provide fine control and consistent lifting power helps prevent cargo damage and accidents due to sudden load shifts. Moreover, the integration of anti-sway and load monitoring systems has further enhanced the safety of these operations.
Enhancing Training and Operational Awareness
Operator-Friendly Interfaces
Hydraulic deck machinery systems are designed with user-friendly interfaces, often featuring digital displays and control panels that provide real-time data on load limits, pressure levels, and system diagnostics. This immediate feedback helps operators make informed decisions and reduces the likelihood of errors during critical operations.
Clear operational guidelines and intuitive control layouts minimize the learning curve for new operators and allow for safer handling of complex machinery.
Facilitating Safety Training
With standardized hydraulic systems onboard, training programs can be streamlined and focused on key safety aspects. Simulation-based training and digital control systems make it easier to train crew members without exposing them to actual operational risks. As a result, better-trained personnel are more capable of identifying warning signs of equipment failure and responding appropriately in emergency situations.
Compliance with Safety Standards and Regulations
Meeting International Maritime Standards
Hydraulic deck machinery used on commercial and naval vessels is subject to rigorous safety standards established by regulatory bodies such as the International Maritime Organization (IMO), the American Bureau of Shipping (ABS), and others. These standards cover areas such as material quality, performance, emergency readiness, and system redundancy.
By using compliant hydraulic systems, operators ensure their vessels meet legal safety requirements, avoiding penalties and improving the overall safety record of their operations.
Regular Inspection and Certification
Many hydraulic systems require periodic inspection and certification to remain operational. These inspections include checking for fluid leaks, pressure irregularities, component wear, and system responsiveness. Routine inspections help identify and resolve potential safety risks before they result in accidents or equipment failure.
Reducing Long-Term Risks and Maintenance Hazards
Fewer Mechanical Failures
Compared to purely mechanical or electric systems, hydraulic machinery tends to experience fewer wear-related issues due to the smooth motion provided by fluid power. This results in fewer unexpected breakdowns and maintenance emergencies, which are often safety risks themselves due to the urgency and complexity involved.
Safer Maintenance Procedures
Hydraulic deck machinery is often modular, allowing components to be isolated and serviced without dismantling the entire system. This reduces the time technicians are exposed to heavy components and pressurized systems, enhancing maintenance safety. Furthermore, depressurization valves and lockout-tagout protocols provide additional safety layers during servicing.
Conclusion
Hydraulic deck machinery is not just a tool of operational efficiency—it is a cornerstone of maritime safety. Through its ability to minimize manual handling, provide precise control, enable remote operation, and function reliably in harsh environments, hydraulic systems significantly reduce the risks associated with deck operations. Safety-enhancing features like overload protection, backup systems, and operator-friendly controls further ensure that tasks are executed without incident.
When properly maintained and operated by trained personnel, hydraulic deck machinery contributes to a safer, more efficient marine environment. For shipowners, operators, and crews, investing in high-quality hydraulic systems and comprehensive safety protocols is not just a compliance requirement—it’s a commitment to protecting lives at sea.
For more insightful articles related to this topic, feel free to visit bdnews55