The rapid evolution of automation technology ha s led to the widespread adoption of Collaborative Robots (Cobots) and Autonomous Mobile Robots (AMRs) in manufacturing and logistics industries. These two types of automation solutions provide significant benefits when integrated, including improved efficiency, flexibility, and cost savings. However, ensuring a seamless integration of Cobots and AMRs requires careful planning, robust technology selection, and strategic implementation.
This article explores the best practices for to maximize operational efficiency while maintaining safety and adaptability in industrial environments.
Understanding Cobots and AMRs
Collaborative Robots (Cobots)
Cobots are designed to work alongside human operators, assisting in various tasks such as assembly, packaging, material handling, and quality inspection. Unlike traditional industrial robots, Cobots are equipped with advanced sensors and AI-driven controls, enabling safe interaction with human workers.
Autonomous Mobile Robots (AMRs)
AMRs are self-navigating robots that transport goods and materials within warehouses, factories, and distribution centers. Unlike Automated Guided Vehicles (AGVs), AMRs use AI, sensors, and dynamic pathfinding to move independently without fixed tracks.
When combined, Cobots and AMRs enhance operational efficiency by creating fully autonomous workflows, reducing human intervention, and improving safety.
Best Practices for Cobot and AMR Integration
1. Define Clear Objectives and Use Cases
Before integrating Cobots and AMRs, it is essential to define clear goals. Common objectives include:
- Reducing manual handling of goods
- Increasing production efficiency
- Minimizing workplace injuries
- Optimizing material flow within the facility
Use case identification helps align technology investments with operational needs, ensuring maximum return on investment (ROI).
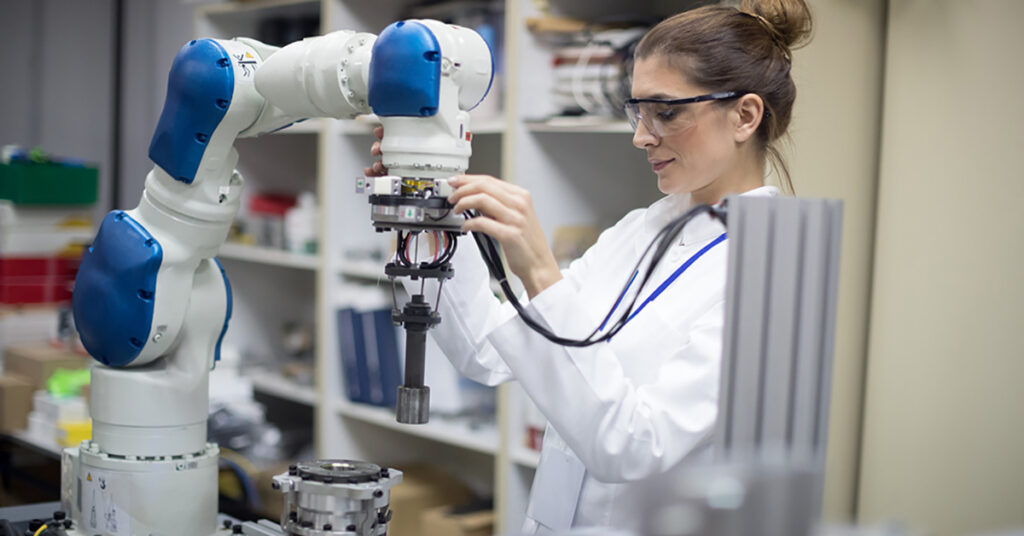
2. Select Compatible Technologies
Successful integration requires selecting Cobots and AMRs that are technologically compatible. Consider the following factors:
- Communication Protocols: Ensure that both systems support the same communication standards (e.g., MQTT, ROS, OPC UA).
- Interoperability: Use open APIs and middleware solutions to enable seamless data exchange.
- Payload Capacity: Verify that Cobots and AMRs can handle the required weight and volume for specific tasks.
3. Establish a Centralized Control System
A unified Warehouse Management System (WMS) or Manufacturing Execution System (MES) should coordinate Cobots and AMRs. The system should:
- Monitor real-time robot status
- Optimize task assignments
- Adjust workflows based on demand fluctuations
- Enable predictive maintenance alerts
4. Implement Seamless Communication Protocols
For smooth integration, Cobots and AMRs must exchange real-time data regarding task progress, location, and environmental conditions. This can be achieved by:
- Using cloud-based IoT platforms for centralized data storage and retrieval.
- Implementing edge computing to process data locally and reduce latency.
- Employing AI-driven analytics to optimize decision-making processes.
5. Optimize Workflow Design
Proper workflow design ensures efficient collaboration between Cobots and AMRs. Key considerations include:
- Path Optimization: Minimize congestion by mapping out optimal AMR travel paths.
- Task Prioritization: Assign priority levels to tasks based on urgency and resource availability.
- Error Handling Mechanisms: Implement automatic recovery strategies in case of disruptions.
6. Ensure Safety and Compliance
Safety is a top priority in any robotic integration. To prevent accidents and ensure compliance with industry regulations:
- Equip Cobots and AMRs with collision detection sensors and LIDAR technology.
- Define safe zones and restricted areas using geofencing.
- Conduct regular safety audits and compliance checks per OSHA, ISO, and ANSI standards.
7. Implement Scalable and Flexible Solutions
A successful integration should be future-proof. Consider:
- Modular designs that allow easy upgrades.
- AI-driven adaptive learning for Cobots and AMRs to improve performance over time.
- Cloud-based fleet management for remote monitoring and scalability.
8. Train Workforce for Human-Robot Collaboration
To maximize efficiency, employees must be trained to work alongside Cobots and AMRs. Training programs should cover:
- Robot operation and troubleshooting
- Emergency stop procedures
- Data analytics interpretation
- Continuous improvement methodologies
9. Monitor and Optimize Performance
After integration, continuous monitoring ensures sustained efficiency. Utilize:
- Real-time analytics dashboards to track performance KPIs.
- AI-based predictive maintenance to prevent unexpected downtime.
- Regular feedback loops to refine automation processes.
Challenges and How to Overcome Them
1. High Initial Investment Costs
- Solution: Start with pilot projects before full-scale deployment. Leverage leasing options and government incentives for automation.
2. Technical Complexity
- Solution: Partner with experienced system integrators and use plug-and-play solutions where possible.
3. Workforce Resistance to Automation
- Solution: Involve employees in planning and provide upskilling opportunities.
4. Cybersecurity Risks
- Solution: Implement robust cybersecurity measures, including data encryption and multi-factor authentication.
Future Trends in Cobot and AMR Integration
1. AI-Powered Decision-Making
AI will enhance decision-making by predicting demand, optimizing workflows, and improving accuracy in task execution.
2. 5G Connectivity for Real-Time Operations
5G will enable ultra-low latency communication between Cobots, AMRs, and cloud systems, enhancing operational efficiency.
3. Edge Computing for Faster Processing
Edge computing will allow Cobots and AMRs to process data locally, reducing dependency on cloud networks.
4. Autonomous Swarm Robotics
Future AMR deployments may involve swarm robotics, where multiple AMRs collaborate dynamically for optimized operations.
5. Sustainable Automation Solutions
Eco-friendly AMRs powered by energy-efficient batteries and Cobots designed for minimal energy consumption will drive sustainable automation initiatives.
Conclusion
Integrating Cobots and AMRs offers transformative benefits, enhancing operational efficiency, safety, and scalability. However, successful implementation requires meticulous planning, technology compatibility, robust safety measures, and continuous optimization.
By following the best practices outlined in this article, businesses can ensure a seamless and efficient integration of Cobots and AMRs, paving the way for a highly automated and intelligent industrial environment.